AJA systems: Difference between revisions
fixed heading levels, some typos |
|||
Line 1: | Line 1: | ||
{{Infobox tool | {{Infobox tool | ||
|image = Tool AJA2.jpg | |image = Tool AJA2.jpg | ||
|toolfullname = | |toolfullname = AJA Orion | ||
|website = http://www.ajaint.com/ | |website = http://www.ajaint.com/atc-orion-series-sputtering-systems.html | ||
|company = AJA INTERNATIONAL INC. | |company = AJA INTERNATIONAL INC. | ||
|description = Thin film deposition and milling systems | |description = Thin film deposition and milling systems | ||
|location = 03.2.218 | |location = 03.2.218 | ||
|primary = | |primary = Karolis | ||
|secondary = | |secondary = Shiv | ||
}} | }} | ||
For the tools' maintenance log, click [[AJA Systems maintenance log|here]]. | For the tools' maintenance log, click [[AJA Systems maintenance log|here]]. | ||
= Overview = | == Overview == | ||
Systems 1 and 2 are identical in terms of operating procedures. The password for logging in is | Systems 1 and 2 are identical in terms of operating procedures. The password for logging in is ''apex''. | ||
= Currently loaded materials = | They differ slightly in their outfitting: | ||
* System 1: Two DC sputtering targets, heater in sample mount and Kaufman ion source for cleaning. Mechanically clamped to the loading arm as well as the rotation holder inside the chamber. | |||
* System 2: One DC sputtering target, and one RF sputtering target, an RF supply to substrate as well as a Kaufman ion source for cleaning. No heater. Mechanically clamped to the loading arm and magnetically clamped to the rotation holder inside. | |||
== Currently loaded materials == | |||
The materials currently available for deposition are as follows: | The materials currently available for deposition are as follows: | ||
Line 132: | Line 131: | ||
Systems 1 and 2 are expected to at least reach a vacuum of about 1x10<sup>-8</sup> Torr and 2x10<sup>-8</sup> Torr after pumping for 24 hours on main chamber, respectively. | Systems 1 and 2 are expected to at least reach a vacuum of about 1x10<sup>-8</sup> Torr and 2x10<sup>-8</sup> Torr after pumping for 24 hours on main chamber, respectively. | ||
= '''Step by step guide''' = | == '''Step by step guide''' == | ||
Various procedures on the system are described in a step by step guide below: | Various procedures on the system are described in a step by step guide below: | ||
Line 353: | Line 352: | ||
* '''Photolith AZ1505''' millrate is approximately '''15nm/min''' (at angle 30 degrees). | * '''Photolith AZ1505''' millrate is approximately '''15nm/min''' (at angle 30 degrees). | ||
=Purchasing= | ==Purchasing== | ||
Materials for evaporation can be bought from many sources, e.g. | Materials for evaporation can be bought from many sources, e.g. | ||
* http://www.espimetals.com/index.php | * http://www.espimetals.com/index.php | ||
Line 364: | Line 363: | ||
Type: G-1650 16.5" OD CF Copper Gasket, Package of 1 | Type: G-1650 16.5" OD CF Copper Gasket, Package of 1 | ||
=Maintenance= | ==Maintenance== | ||
The standard configurations on the systems are: | The standard configurations on the systems are: | ||
[[Image:configuration_system1.jpg|thumb|center|600px|Configuration settings on system 1]]<BR> | [[Image:configuration_system1.jpg|thumb|center|600px|Configuration settings on system 1]]<BR> |
Revision as of 15:34, 12 February 2019
![]() | |
Essentials | |
---|---|
Full name | AJA Orion |
Manufacturer | AJA INTERNATIONAL INC. |
Description | Thin film deposition and milling systems |
Location | 03.2.218 |
Responsibility | |
Primary | Karolis |
Secondary | Shiv |
For the tools' maintenance log, click here.
Overview
Systems 1 and 2 are identical in terms of operating procedures. The password for logging in is apex.
They differ slightly in their outfitting:
- System 1: Two DC sputtering targets, heater in sample mount and Kaufman ion source for cleaning. Mechanically clamped to the loading arm as well as the rotation holder inside the chamber.
- System 2: One DC sputtering target, and one RF sputtering target, an RF supply to substrate as well as a Kaufman ion source for cleaning. No heater. Mechanically clamped to the loading arm and magnetically clamped to the rotation holder inside.
Currently loaded materials
The materials currently available for deposition are as follows:
|
|
|
Systems 1 and 2 are expected to at least reach a vacuum of about 1x10-8 Torr and 2x10-8 Torr after pumping for 24 hours on main chamber, respectively.
Step by step guide
Various procedures on the system are described in a step by step guide below:
(An illustrated guide for new users by Mingtang: File:How to Evaporate metal in AJA1.pdf. A physical copy of the same lies by the tool.)
Loading your sample
- Check the cryo-pump monitor. It should be between 12-17 K. If it's higher than 20 K, grab an ansvarlig or a technical staff member.
- Check that the turbo frequency is 1500 Hz. The turbo pumps on the load lock.
- Check that the pressure in the main chamber (ion gauge sensor) is <1x10-7 Torr
- Check that the load lock gate valve (connects the load lock to the main chamber) is closed
- Push down the 'Load Lock' switch in order to vent the load lock
- Once the load lock pressure reaches ~740 Torr, the load lock lid pops out a bit and can be rotated freely.
- Do not apply force and pull the load lock lid out. The load lock may not be vented yet.
- Rotate the lid until the permanent markers meet and twist the lid out, pivoting about the two permanent marks on the left.
- The permanent marks indicate the position of spring loaded ball bearing that hold the lid in place, preventing it from falling out.
- Ideally, you want rotate the lid so as to pivot against two bearings.
- Place the load lock lid, handle up, on the three rubber bumps.
- Remove the sample cassette. It's held in place by three pins that lock into a groove
- Examine the sample cassette. There are three small pins. These pins, via a similar mechanism lock onto the holder inside the main chamber.
- Grab a fresh cleanroom wipe, place the sample cassette on the wipe.
- Load your chip either using the mechanical clamps or the double sided Kapton tape. Carbon tape is being phased out as it may be a source of unwanted residues inside the chamber and on the metals.
- Load the sample cassette inside the load lock, rotate the holder to confirm all three pins are locked in place, replace the lid and flick the 'load lock' switch up to pump out.
- Wait till the chamber pressure goes down to 3x10-6 Torr. The turbo will have revved up to 1500 Hz by now. Confirm this.
- Open the gate valve between the main chamber and the load lock.
- Load your sample. The mechanism which locks the sample cassette on to the holder in the main chamber, also simultaneously unlocks it from the loading arm.
- Take note of the sample cassette orientation on the holder as well as the rotation/orientation of the loading arm. In principle, you should unload using the same orientation as this will be the easiest.
- Close the load lock valve.
- Check main chamber vacuum
- Check cryo pump temp
Evaporating metal
- Rotate the sample holder to face the crucible liners
- Choose the material on the linear crucible drive as well as on the deposition controller.
- Open the ebeam shutter by flicking the physical ebeam shutter switch to open.
- This exposes the metal to be evaporated.
- If you don't open this shutter, the accelerated focussed electron beam will hit the shutter instead of the metal and drill a hole through it!
- Switch on the Carrera Ferro Tec high voltage power supply. The switch is green and is labelled 'Main'.
- Turn on the high voltage. It sets the beam acceleration voltage to 10 kV. This is fixed and not changed by the users.
- Be very sure that you have opened the ebeam shutter.
- Two clicks of the knob and the current set point is set to 4 mA.
- Wait till the current increases to this value.
- Can you see the bright spot where the beam hits the metal in the crucible.
- Center the beam and make sure the beam is neither too focused nor too defocused.
- Now, consult the excel log sheet to determine the typical current needed to get a finite evaporation rate.
- Ramp the current up at about 20 mA/min to half the value. Let it sit at that value for 2 mins while the metal soaks and thermally equilibrates.
- Too fast and you'll crack the crucible liner
- or your evaporated metal film will be rough
- 1 A/s is a good rate for metal film evaporation. Try and stay around this value.
- When you are ready to evaporate, zero the counter on the deposition controller and open the sample shutter.
- The shutter takes about 1-2 secs to open, so you don't have to be paranoid about synchronizing the zero with the shutter opening.
- Wait until the right thickness is evaporated.
- Close the substrate shutter.
- Ramp the beam down to 0 in a period of a min. Don't be too quick about it. We want the metal and the liner to cool down slowly to stop the liner from cracking due to stress.
- Wait 2 mins for the metal to cool down before moving over to the next metal
- If you're done, turn off the Carrera voltage supply.
- Turn off high voltage if you are done evaporating.
- Close the ebeam shutter if the metal is no longer red hot.
Unloading your sample
- Rotate the sample to the correct position (same orientation as during the loading procedure)
- Open the load lock gate valve, and unload your sample
- Close the load lock valve.
- Vent the load lock using the load lock switch on the main rack.
- As before, wait till the load lock reaches ~740 Torr and pops out a bit.
- Twist and pull the lid out if the permanent marks are lined up.
- Rest the lid on rubber knobs, handle up
- Fresh cleanroom wipe!
- Get the sample cassette out, unload your sample.
- If you used a double sided tape, wipe off the residue with IPA or Ethanol
- Put the sample cassette back and pump out the load lock.
- Fill out the excel log file
- Clean up after yourself. If the work station is found untidy, the last user will be held accountable.
Using the Kaufman ion source (ion milling)
- Load your sample via the load lock following the procedure detailed above
- Turn off the ion gauge (pressure gauge).
- On the laptop, make sure the PhaseIIJ programs is running. If not start it up.
- The password:apex
- Set the adaptive pressure controller to 'Remote'
- It's a 3 sec long press.
- In the program, turn on the Ar flow and set the 'STPT' (set point) to an appropriate value.
- Look at the excel log files to select a relevant set of values for the flow. The flow roughly sets the base Ar pressure in the chamber.
- Select 'Pressure' button and enter a value:
- Again, the excel log files should guide you in selecting an appropriate value. Typically, a flow of 6 sccm and a pressure of 0.6 mbar works nicely.
- The program floors the entered value to a single digit precision. 0.61 will become 0.6. 0.6 sometimes becomes 0.5. I just live with this minor annoyance.
- A PID controlled gate valve between the cryo pump and the chamber will adjust so that the Ar pressure in the chamber matches the set point. You'll hear the valve adjusting when you set the controller to remote. On the adaptive pressure controller display look at the 'SP' and the 'P1'. These should match the value that you want and keyed into the phaseIIJ program.
- Rotate the sample to face the ion milling gun
- Turn on the Kaufman ion source controller power supply.
- Select a relevant beam voltage and beam mA values.
- Consult the excel log file.
- 300V and 23 mA is the default setting
The default values are printed out and taped below the Kaufman controller. Make sure you key in the default values once you're done with the system
- System specific instructions:
AJA1:
- Click on the ion gas button. It should be green. This diverts the Ar gas flow to the gun.
- Click on the 'output' button to turn on the gun.
- This fires the Ar ions. The ion source shutter still protects your sample.
- Wait for the indicator to turn purple.
- You can trigger this Kaufmann shutter with the 'shutter' button and start your timer
- You are now milling
AJA2:
- Click on the 'output' button to turn on the gun.
- This fires the Ar ions. The ion source shutter still protects your sample.
- Wait for the indicator to turn purple.
- You can trigger this Kaufmann shutter with the 'shutter' button and start your timer
- You are now milling
- To turn off the Kaufman ion source click the green output button. It should turn red.
- Wait 15 s for the gun to cool down
- In the pressure control section of the program, click 'Open' to completely open the cryo gate valve and pump the Ar out.
- Turn off the Ar gas flow.
- Turn off the Kaufman source controller
- Set the adaptive pressure controller to local
- Turn on the ion gauge (pressure sensor).
- Proceed with evaporating metal or unloading your sample following the guidelines listed in the sections above.
Sputtering metals
- Load your sample via the load lock following the procedure detailed above
- Turn off the ion gauge (pressure gauge).
- On the laptop, make sure the PhaseIIJ programs is running.
- If not start it up. The password:apex
- Set the adaptive pressure controller to 'Remote'
- It's a 3 sec long press.
- info: Finer control over the Ar pressure in the chamber is achieved by selecting 'Pressure' button and entering a value.
- info: In the program, turn on the Ar flow and set the 'STPT' (set point) to an appropriate value.
- Look at the excel log files to select a relevant set of values for the flow. The flow roughly sets the base Ar pressure in the chamber.
- info: Finer control over the Ar pressure in the chamber is achieved by selecting 'Pressure' button and entering a value.
- Again, the excel log files should guide you in selecting an appropriate value.
- The program floors the entered value to a single digit precision. 0.61 will become 0.6. 0.6 sometimes becomes 0.5. I just live with this minor annoyance.
- info: A PID controlled gate valve between the cryo pump and the chamber will adjust so that the Ar pressure in the chamber matches the set point. You'll hear the valve adjusting when you set the controller to remote. On the adaptive pressure controller display look at the 'SP' and the 'P1'. These should match the value that you want and keyed into the phaseIIJ program.
- Rotate the sample to face downwards.
- The sputter sources are angled a bit and 10-20 degree might give you a more head on sputtering.
- Power up the relevant sputtering source power unit.
- Striking the plasma:
- Open the substrate shutter. The sputter sources have individual shutters.
- Set the Ar flow to 80 sccm and pressure to 30 mTorr.
- Set the RF2 (sputtering target) stpt to 50 W and turn on the output.
- Once the plasma ignites, the pressure can be lowered to 2-4 mTorr and flow to 20 sccm.
- Check that the plasma is visible (a faint purple blueish hue inside the main chamber).
- There is a little pink indicator in the software that should light up in the control software congruent with when the plasma is visible in the chamber.
- Ramping: Enter the ramp time first and then the new set point such that the ramp rate is 1 W/s. Hit enter or click away after entering the new set point.
- Entering the new set point before entering the ramp time will result in the system jumping to the set point in one step. This will cause rapid heating and will break the sputter housing.
- Close the viewport shutter, since they will get covered with the sputtered film.
- Once the desired set point is reached, open the sputter shutter and start the timer.
- Ramping down:
- Enter the ramp down time and THEN the set point of 50 W.
- Once the system ramps down to 50 W, turn off the output.
- Open the adaptive pressure controller by clicking on 'Open' in the software.
- This opens up the cryo valve to max.
- Turn off the Ar gas flow.
- Set the adaptive pressure controller to local
- Turn on the ion gauge
- Carry on with other steps such as metallization, unloading, etc as outlined above.
For safe operation of the rf ALWAYS enter a ramp rate such that the rf circuitry never ramps faster than 1W/second. Enter ramp rate BEFORE changing wattage!
Substrate sputtering (RF)
- Load your sample via the load lock following the procedure detailed above
- Turn off the ion gauge (pressure gauge).
- On the laptop, make sure the PhaseIIJ programs is running.
- If not start it up. The password:apex
- Set the adaptive pressure controller to 'Remote'
- It's a 3 sec long press.
- Rotate the sample to face downwards.
- Power up the relevant sputtering source power unit.
- Auto:
- Select run process
- Scroll down to the desired program
- Run
- Manual:
- Striking the plasma:
- Set the Ar flow to 80 sccm and pressure to 30 mTorr.
Info:
A PID controlled gate valve between the cryo pump and the chamber will adjust so that the Ar pressure in the chamber matches the set point. You'll hear the valve adjusting when you set the controller to remote. On the adaptive pressure controller display look at the 'SP' and the 'P1'. These should match the value that you want and keyed into the phaseIIJ program.
The program floors the entered pressure set point value to a single digit precision. 0.61 will become 0.6. 0.6 sometimes becomes 0.5. I just live with this minor annoyance.
- Striking the plasma (contd.):
- Set the RF1 stpt to 25 W and turn on the output.
- Once the plasma ignites, the pressure can be lowered to 2-4 mTorr and flow to 20 sccm.
- Check that the plasma is visible (a faint purple blueish hue inside the main chamber).
- There is a little pink indicator in the software that should light up in the control software congruent with when the plasma is visible in the chamber.
- Ramping: Enter the ramp time first and then the new set point such that the ramp rate is 1 W/s. Hit enter or click away after entering the new set point.
- Max set pt is 50 W
- Entering the new set point before entering the ramp time will result in the system jumping to the set point in one step. This will cause rapid heating.
- Close the viewport shutter.
- Once the desired set point is reached start the timer.
- Ramping down:
- Enter the ramp down time and THEN the set point of 25 W.
- Once the system ramps down to 25 W, turn off the output.
- Open the adaptive pressure controller by clicking on 'Open'.
- This opens up the cryo valve to max.
- Striking the plasma (contd.):
- After Auto or Manual:
- Turn off the Ar gas flow.
- Set the adaptive pressure controller to local
- Turn on the ion gauge
- Turn off the RF power source
- Carry on with other steps such as metallization, unloading, etc as outlined above.
Older ion milling notes
When operating normally, the chamber should light a clear whiteish hue, and the kaufman power source should read numbers similar to these:
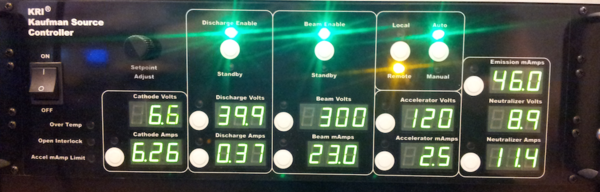
Miscellaneous notes / values for milling
Please update this list with good tips / mill rates for materials:
- The approximate mill rate for InSb heterostructure is 15 nm/min. It is advised to tilt the sample to 30 degrees and use 30 speed on the rotating engine. This gives a cleaner and more smooth surface.
- Photolith AZ1505 millrate is approximately 15nm/min (at angle 30 degrees).
Purchasing
Materials for evaporation can be bought from many sources, e.g.
The boats we use approximately take 50g of material. Material should be high purity (about 3-4N ~ 9.999% purity). Preferably buy nuggets or pellets, sizes 1/8" ~ 3-6mm in size.
For ordering of copper gaskets:
Type: G-1650 16.5" OD CF Copper Gasket, Package of 1
Maintenance
The standard configurations on the systems are:
If you are unable to ignite the plasma (either dc, rf or ion plasma) start by checking for shorts between pins on the powersupply input on the sputtering arm / ion source.